The Facts About Premier Aluminum Llc Uncovered
Table of Contents10 Easy Facts About Premier Aluminum Llc ShownUnknown Facts About Premier Aluminum LlcPremier Aluminum Llc - The FactsA Biased View of Premier Aluminum Llc
(https://comicvine.gamespot.com/profile/premieraluminum/)Making use of reduced cost and unqualified distributors can create top quality problems, and squandered time and cash in the long run. To aid you through the procedure, right here are some things to consider when choosing the ideal steel spreading provider.
For instance, a company that just uses the financial investment casting procedure will certainly attempt to market you on why that process is best for your application. But suppose using the sand casting process is best for you and your needs? Rather, try to find a provider that supplies a series of casting procedures so the very best option for YOU is picked
If functioning with a solitary resource for all of your spreading requires is very important to you, the vendor needs to be diverse in its abilities. When incorporated with other incorporated capacities, this can aid streamline and compress the supply base. When selecting the appropriate spreading vendor, cautious consideration should be provided to top quality, service, and price.
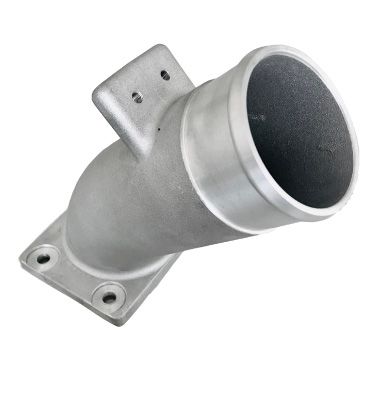
Little Known Facts About Premier Aluminum Llc.
Purchasers increasingly pick casting suppliers that have machining abilities. This can avoid dispute if issues are discovered during machining. If a 3rd party is machining, it might lead to "finger-pointing" concerning who is at mistake. Is it a spreading concern or a machining issue? If the spreading provider discovers a concern during machining, the issue is fixed quicker without any dispute over whose fault it is.
Problem or no, incorporated machining streamlines the supply chain and minimizes taking care of time and delivery price prior to the product makes it to the customer. What do you need from your spreading distributor? Are you looking for somebody to simply deliver a steel component to your front door or do you need extra? As an example, if you do not have in-house metallurgy knowledge, validate that the vendor can offer guidance in choosing the proper alloy based upon your certain application - Casting Foundry.
Some shops are limited or specialized. Make sure the vendor can fulfill all your material or alloy demands to eliminate the need for several suppliers.
About Premier Aluminum Llc
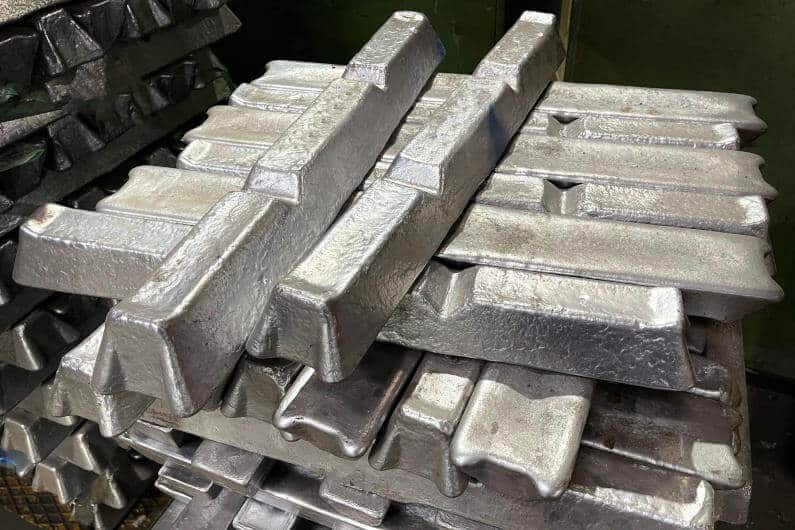
Research the supplier's website. Talk to a sales representative or service partner.
Light weight aluminum is likewise light-weight and has good corrosion resistance, making it perfect for applications where weight and sturdiness are essential factors. Furthermore, aluminum spreading is a cost-effective approach of manufacturing, as it requires much less energy and sources than other methods. Iron casting, on the other hand, entails pouring liquified iron into a mold to create a wanted form.
The 3-Minute Rule for Premier Aluminum Llc
Iron spreading is likewise able to stand up to high temperatures, making it suitable for usage in applications such as engine components and industrial machinery. Nonetheless, iron casting can be extra expensive than light weight aluminum spreading because of the higher cost of basic materials and the power needed to melt the iron. When making a decision in between aluminum spreading and iron spreading, it is very important to take into consideration the specific needs of the application.
If stamina and resilience are extra important, iron casting might be the far better choice. Other factors to think about consist of expense, a knockout post production quantity, and lead time. To conclude, both aluminum casting and iron casting have their very own distinct benefits and negative aspects. By carefully taking into consideration the particular needs of the application, suppliers can choose the very best procedure for their product.ZheJiang Dongrun Spreading Market Co,. Ltd was built in 1995, We have actually remained in the casting market for more than 25 years. Pass away spreading is the name offered to the
procedure of producing complex steel parts with use of molds of the component, additionally referred to as dies. The process makes use of non-ferrous steels which do not have iron, such as light weight aluminum, zinc and magnesium, because of the desirable residential or commercial properties of the metals such as reduced weight, higher conductivity, non-magnetic conductivity and resistance to rust. Pass away spreading manufacturing is quick, making high production levels of elements very easy.
It creates more parts than any type of other process, with a high degree of precision and repeatability. To discover more regarding die casting and pass away casting products utilized at the same time, continued reading. There are three sub-processes that drop under the group of die casting: gravity die casting (or long-term mold and mildew casting), low-pressure die spreading and high-pressure die casting. The pure steel, additionally known as ingot, is added to the heater and kept at the molten temperature of the metal, which is then transferredto the shot chamber and infused into the die. The stress is after that maintained as the steel solidifies. Once the steel solidifies, the cooling process starts. The thicker the wall surface of the part, the longer the cooling time as a result of the amount of interior steelthat additionally requires to cool. After the component is totally cooled down, the die cuts in half open and an ejection mechanism pushes the element out. Following the ejection, the die is closed for the following shot cycle. The flash is the added material that is cast during the process. This must be cut off using a trim device to
leave just the main part. Deburring eliminates the smaller sized pieces, called burrs, after the trimming process. The element is polished, or burnished, to provide it a smooth coating. However, this proved to be an imprecise test, because the tester might reduce right into an item and miss out on a location with porosity. Today, top makers use x-ray testing to see the entire interior of components without cutting into them. This allows them to much more properly approve or deny parts. To reach the finished product, there are three main alloys used as die spreading product to choose from: zinc, aluminum and magnesium. Zinc is one of one of the most pre-owned alloys for die casting as a result of its reduced expense of raw materials.